Your cart is currently empty!
HMI + PLC Combo Units
Our HMC series combines a touchscreen HMI and PLC all in one unit. Utilized worldwide to employ diverse applications, our HMI+PLCs lower costs, save space, and feature options including: Serial and Ethernet communication, support for Class I Division 2 installations, and numerous I/O configurations. What’s more, they provide an affordable combination of display and control in a single package and programmed by using our Free HMI+PLC software MAPware-7000 with graphs, alarms, trending, data logging, web server functionality and more.
Watch step by step how to unlock additional software functionality in our advanced HMC models such as MQTT, VNC Server, email, advanced graphics, recipe database, and much more.
Results
-
4.3″ Advanced HMI + PLC
HMC4043A-M- Recommended choice for new projects compared to HMC2043A-M
- 480 x 272 Resolution, 1 Ethernet Port, 1 USB Port, 1 Serial Port
- 1 slot for I/O expansion module
- Free Configuration Software, VNC Server, FTP Server, MQTT, Email, Barcode Scanner
- cULus, Class I Division 2, IP66, CE, RoHS
$410.00Quantity Discounts Available -
I/O Module | 12 Bi-Directional Digital Inputs, 12 Digital Outputs, 2 Analog Inputs
HMC3-M1212Y0200-V2- 12 Bi-Directional Digital Inputs (2 High Speed (Quadrature, Standard))
- 12 Digital Outputs (10 Relay, 2 PNP, 1 PWM (Normal, CW/CCW, Pulse/Direction and Fixed Pulse))
- 2 Analog Inputs (Voltage: 0-5V, 0-10V Current:0-20mA, 4-20mA)
- Class I, Division 2 Rated, UL Listed, CE Certified
$165.00Quantity Discounts Available -
I/O Module | 12 Bi-Directional Digital Inputs, 10 Digital Outputs, 2 Analog Inputs, 1 Analog Output
HMC3-M1210Y0201-V2- 12 Bi-Directional Digital Inputs (2 High Speed (Quadrature, Standard))
- 10 Digital Outputs (8 Relay, 2 PNP, 1 PWM (Normal, CW/CCW, Pulse/Direction and Fixed Pulse))
- 2 Analog Inputs (Voltage: 0-5V, 0-10V Current: 0-20mA, 4-20mA)
- 1 Analog Output (Voltage: 0-5V, 0-10V Current: 0-20mA, 4-20mA)
- Class I, Division 2 Rated, UL Listed, CE Certified
$180.00Quantity Discounts Available -
4.3″ Standard HMI + PLC
HMC2043A-M- Easy conversion for upgrading HMC3000 Series projects that were programmed using IEC Programming Language
- 480 x 272 Resolution, 1 Ethernet Port, 1 USB Port, 1 Serial Port
- 1 slot for I/O expansion module
- Free Configuration Software, Data Logging, Trend Graphics, RTC, Recipes, Meters & Bar Graphs
- cULus, Class I Division 2, CE, RoHS, IP66
$410.00Quantity Discounts Available -
7.0″ Advanced HMI + PLC
HMC4070A-M- Recommended choice for new projects compared to HMC2070A-M
- 800 x 480 Resolution, 1 Ethernet Port, 1 USB Port, 2 Serial Port
- 3 slots for I/O expansion modules
- Free Configuration Software, VNC Server, FTP Server, MQTT, Email, Barcode Scanner
- cULus, Class I Division 2, IP66, CE, RoHS
$550.00Quantity Discounts Available -
7.0″ Standard HMI + PLC
HMC2070A-M- Easy conversion for upgrading HMC3000 Series projects that were programmed using IEC Programming Language
- 800 x 480 Resolution, 1 Ethernet Port, 1 USB Port, 2 Serial Port
- 3 slots for I/O expansion modules
- Free Configuration Software, Data Logging, Trend Graphics, RTC, Recipes, Meters & Bar Graphs
- cULus, Class I Division 2, CE, RoHS, IP66
$550.00Quantity Discounts Available -
10.1″ Advanced HMI + PLC
HMC4101A-M- 1024 x 600 Resolution, 1 Ethernet Port, 1 USB Port, 2 Serial Port
- 5 slots for I/O expansion modules
- Free Configuration Software, VNC Server, FTP Server, MQTT, Email, Barcode Scanner
- cULus, Class I Division 2, IP66, CE, RoHS
$865.00Quantity Discounts Available -
I/O Module | 12 Bi-Directional Digital Inputs, 10 PNP Digital Outputs, 2 Analog Inputs, 1 Analog Output
HMC3-M1210P0201-V2- 12 Bi-Directional Digital Inputs (2 High Speed (Quadrature, Standard))
- 10 PNP Digital Outputs (1 PWM (Normal, CW/CCW, Pulse/Direction and Fixed Pulse))
- 2 Analog Inputs (Voltage: 0-5V, 0-10V Current: 0-20mA, 4-20mA)
- 1 Analog Output (Voltage: 0-5V, 0-10V Current: 0-20mA, 4-20mA)
- Class I, Division 2 Rated, UL Listed, CE Certified
$180.00Quantity Discounts Available -
I/O Module | 12 Bi-Directional Digital Inputs, 12 PNP Digital Outputs, 2 Analog Inputs
HMC3-M1212P0200-V2- 12 Bi-Directional Digital Inputs (2 High Speed (Quadrature, Standard))
- 12 PNP Digital Outputs (1 PWM (Normal, CW/CCW, Pulse/Direction ad Fixed Pulse))
- 2 Analog Inputs (Voltage: 0-5V, 0-10V Current: 0-20mA, 4-20mA)
- Class I, Division 2 Rated, UL Listed, CE Certified
$165.00Quantity Discounts Available -
I/O Module | 16 Bi-Directional Digital Inputs, 14 Digital Outputs
HMC3-M1614Y-V2- 16 Bi-Directional Digital Inputs (2 High Speed (Quadrature, Standard))
- 14 Digital Outputs (12 Relay, 2 PNP, 1 PWM (Normal, CW/CCW, Pulse/Direction and Fixed Pulse))
- Class I, Division 2 Rated, UL Listed, CE Certified
$190.00Quantity Discounts Available -
I/O Module | 16 Bi-Directional Digital Inputs, 16 PNP Digital Outputs
HMC3-M1616P-V2- 16 Bi-Directional Digital Inputs (2 High Speed (Quadrature, Standard))
- 16 PNP Digital Outputs (1 PWM (Normal, CW/CCW, Pulse/Direction and Fixed Pulse))
- Class I, Division 2 Rated, UL Listed, CE Certified
$190.00Quantity Discounts Available -
I/O Module | 8 Bi-Directional Digital Inputs, 8 Digital Outputs, 4 Analog Inputs, 1 Analog Output, Thermo/RTD
HMC3-M0808Y0401T-V2- 8 Bi-Directional Digital Inputs (2 High Speed (Quadrature, Standard))
- 8 Digital Outputs (6 Relay, 2 PNP, 2 PWM (Normal, CW/CCW, Pulse/Direction and Fixed Pulse))
- 4 Analog Inputs (Current, Voltage, RTD, Thermocouple)
- 1 Analog Output (Voltage, Current)
- Class I, Division 2 Rated, UL Listed, CE Certified
$295.00Quantity Discounts Available
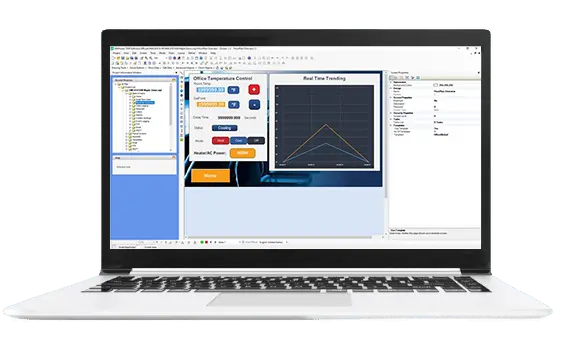
HMI+PLC Configuration Software
MAPware-7000 is the configuration software used to program all our HMI+PLCs. Use just one software application to program both the screens that appear in the display as well as the logic that controls your system. Create projects using the tools and graphic images included with the software to provide a functional user-interface for your control system. In addition, the built-in or expandable I/O can be used to control and monitor your system utilizing the logic instructions integrated in the software.
Our HMI+PLCs support IEC61131-3 program language. The graphics program and logic program work together to provide complete control through the graphic interface.
MAPware-7000 Logic Editing Mode
MAPware-7000 minimizes software development time by making it easy to design & program all aspects of your project in one environment. Stop worrying about if your HMI and PLC are communicating to each other, MAPware-7000 was created to eliminate this frustration and provides one interface to interact with your whole control system.


Why Class 1, Division 2
The first requirement for a Class I enclosure is strength. The enclosure must be strong enough to contain an explosion within. The walls must be wide enough to withstand the internal strain. It must be explosion-proof in case gas or vapors get inside. Secondly, it must function at a temperature below the ignition temperature of the surrounding atmosphere. The equipment must also provide a way for the burning gases to escape from the device as they expand during an internal explosion.
When the hazardous material is expected to be confined within closed containers or closed systems and will be present only through accidental rupture, breakage or unusual faulty operation, the situation could be called “abnormal”. The Code writers have designated these two kinds of conditions very simply, as Division 1 – normal and Division 2 abnormal.
Our HMI + PLC are C1D2 certified and meet strict requirements.
Read our Case Studies
OEM adds functionality with a Maple Systems HMI+PLC combo model
Jake Davis, Product Engineer for De Dietrich Process Systems, Inc contacted us for help with a redesign of the Powder Pump. The Powder Pump is a dense-phase pneumatic conveying system that eliminates the need to manually handle solids and minimizes other potential hazards by providing a closed system to transfer materials such as powders, prills, granules, flakes, etc. in a safe and contained manner. Read how Maple Systems product is used in this real-world application.
Visit our case studies page to see our customers use our products to reduce costs, provide features, increase functionality, and solve problems. It’s easy to see why our customers are so happy with how we do business and continue to use our products year after year.

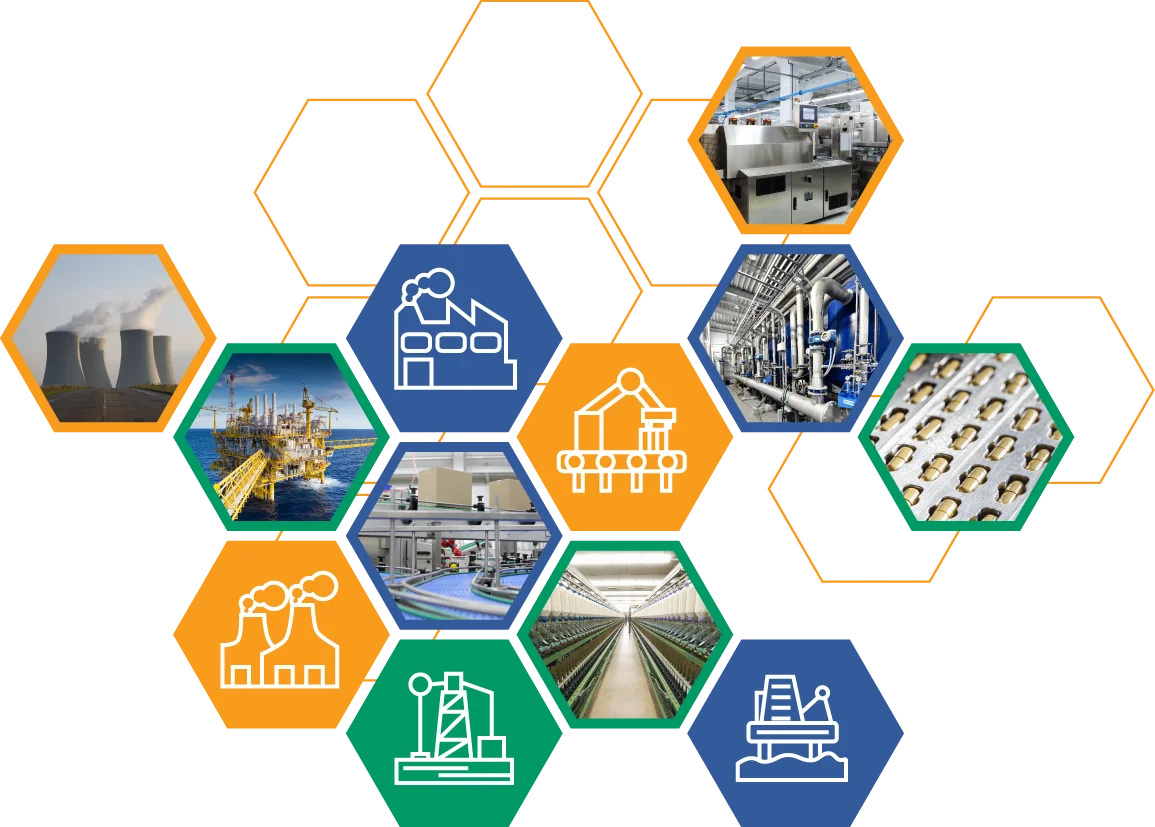
Serving Industries Around the World
Monitor temperatures, pressures and flow rates that can suddenly change
Automated processes can work 24/7 with occasional outages for maintenance, which is clearly faster than human operators can perform. For this reason, increased efficiency and higher through-put rates are two of the biggest benefits of automation. In addition to elevated efficiency, automation also allows companies to collect valuable data from the production line that can be used to improve maintenance. Predictive maintenance is a new approach to maintenance where real-time data is used to identify potential issues and alert when maintenance is needed – further reducing costs as well as production downtimes.
Learn more about the industries we serve and discover why more and more companies are choosing Maple Systems.
Supervisory Control and Data Acquisition (SCADA)
For a local interface at the machine our HMI + PLC units are the ideal solution. This affordably priced units combine a touchscreen display and PLC control in a single package and programmed by using our Free MAPware7000 software with graphs, alarms, trending, data logging, web server functionality and more.
We offer all the components you need to create your own unique level of supervisory data acquisition and control, from the simplest stand-alone machine to sophisticated multi-device networked production line(s), all the way to enterprise-level operations and IIoT functionalities leveraging cloud connectivity.
Add Maple Systems components to grow your abilities to supervise, control, and acquire data.
To learn more about how our products work together to create scalable SCADA solutions, visit our SCADA solutions page.

Additional Resources
Read more about the types of HMIs — as well as their basic functions and new and emerging HMI functions and connectivity options. Additionally, we discuss the role of HMIs in IIoT operations and the trend towards standardization (for both open source and proprietary setups) in our HMI Design Guide.
Read more about remote access at the machine level, seeing/acquiring additional information at a supervisory station, or communicating data outside of your factory local network in our
FREE SCADA and HMI Guide
In our Support Center we have compiled all of our most common technical support questions into one place to help you find the answers you need. From hardware to software, and everything in between, we’ve got you covered.
Customize Your HMI, HMI+PLC, or PC
Highlight your brand and differentiate your machine with a custom label
Company branding is a significant aspect of business marketing. By using custom labels on your products, you can create an identity to gain recognition from customers and potential buyers. It helps consumers recognize that the product was made by your company. Having this type of brand recognition can help your business stand out from competitors. Our Custom Labels:
- Fit Your Product Perfectly
- Offer Professional-Looking Packaging
- Strengthens Your Marketing Efforts
- Provides an Identity to Your Business

HMI + PLC Combo Documentation
Manuals & Guides
Additional Resources
Need additional support?
Visit our FAQ section for more info or contact us to get help from our support team.
Frequently Asked Questions
What is a Human Machine Controller (HMC)?
A Human Machine Controller (HMC or HMI + PLC) combines an HMI and PLC into one unit.
The HMI + PLC can display visualizations on the LCD touch panel as well as run logic control internally. Pluggable I/O can be attached to the back of the unit.
Utilized worldwide in diverse applications, a Maple Systems HMI + PLC offers lower costs, saves space, both Serial and Ethernet communication, and a UL listing plus C1D2 Certification.
Can the HMC be configured as a Modbus TCP master and a slave at the same time?
Yes, the HMC can be configured as a Modbus TCP Master on COM3 and still retain the default Modbus TCP Slave configuration.
You must choose one or the other between master and slave for Modbus RTU, but Modbus TCP can be both simultaneously thanks to Ethernet. As a master (client) you can read Modbus data from, or write Modbus data to, other Modbus TCP devices.
Can a Maple Systems HMI+PLC (HMC) communicate to an Allen Bradley PLC?
Scenario: Customer wants to integrate a Maple Systems HMI+PLC (HMC) solution with a Allen Bradley PLC and a Fanuc robot.
Yes, you can use the Modbus protocol to communicate to an Allen Bradley PLC and a Fanuc robot from a Maple Systems HMI+PLC (HMC). All the tags and IO would need to be mapped manually.
Our HMI+PLC (HMC) communicate with device that uses the Modbus RTU/TCP protocol. Visit of Support Center for downloadable Controller Information sheets (search for Modbus) to walk you through the set-up.
Can I pair an HMI+PLC (HMC) with a Maple Systems PLC?
Absolutely. Maple Systems PLCs can communicate with an HMI + PLC (HMC) either with or without I/O modules attached to it.
A potential application would be to have the PLC installed in a remote cabinet, while the HMC is mounted in a convenient location for the operator. With the HMC optional I/O modules, local control switches could be monitored and controlled by the HMC to reduce wiring complexity.
Additionally, only one configuration software is required to program both units pieces. In IEC mode, Modbus is used to communicate between the PLC and HMC.
Do the Maple Systems HMI+PLCs (HMC) support Pulse Width Modulation (PWM)?
Yes. Our HMI+PLCs (HMC) support Pulse Width Modulation in MAPware-7000.
See the specific Series IO Module guide for more information specifics on which IO modules support Pulse Width Modulation (PWM) and what registers are used for configuration.
Four modes of PWM are supported for most IO modules; Normal, Clockwise/Counter-Clockwise (CW/CCW), Pulse/Direction, and Trapezoidal (Fixed Pulse). When using PWM outputs, different product lines have different maximum frequencies ranging from 1 kHz to 200 kHz.
Tech Note 7009, “Pulse Width Modulation”, describes each of the four types of PWM output, and then lists which registers to configure, how to configure those registers, and the minimum and maximum ranges of each register.
Review the IO module specification sheets to ensure PWM is available.
Do the Maple Systems HMI+PLCs (HMC) support High-Speed Counters (HSC)?
Yes. Our HMI+PLCs (HMC) support High-Speed Counters in MAPware-7000.
See the specific Series IO Module guide for more information on which IO modules support High-Speed Counters (HSC) and what registers are used for configuration.
Most supported IO modules offer 2 or 4 high speed inputs. Both quadrature and standard HSCs are supported. When using HSCs, different product lines have different maximum frequencies ranging from 10 kHz to 200 kHz.
Can I do Remote Access with my HMI+PLC?
Yes. Ethernet HMI+PLC models allow you to create Web Screens which are accessible through a web browser on the local network.
Additionally, you can pair one of our cMT Gateway products with a Maple Systems HMI + PLC (HMC) unit to add remote data access and enhanced data extraction.
The cMT Gateway uses Modbus TCP to pull data from the HMI + PLC combo unit which can then be synched to an SQL database, sent to the cloud using MQTT, or shared with SCADA and ERP systems using OPC UA.
The Gateway can also be configured to send emails with data logs at set times, or when an alarm is triggered. If the EasyAccess 2.0 service is enabled on the Gateway, Web Screens configured for the HMI + PLC in MAPware-7000 become accessible from anywhere in the world!
Do you offer warranty on HMC product? Are they repairable?
We offer a one year warranty on our HMC terminals, 90 day warranty on our I/O Modules. These products are repairable.
What is your standard lead time on the HMC units and their Modules?
We have large amounts of inventory and can typically ship within 1 to 2 business days!